الحار منتجات
ملكنا الإخبارية
ball mill in mine
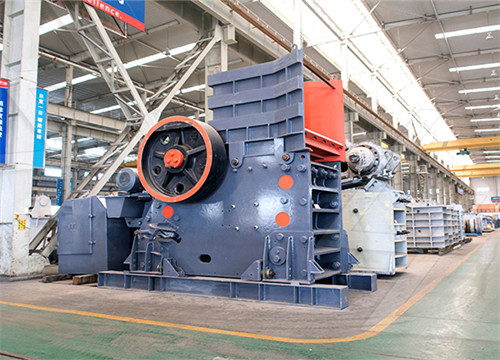
(PDF) Grinding Media in Ball Mills-A Review
2023423 International Journal of Mineral Processing. Farit Urakaev. We will focus on the important aspect of mechanochemical processing by grinding in a ball mill, namely, nanoscale wear of the treated

Integrating geometallurgical ball mill throughput predictions
202321 More specifically, a ball mill throughput prediction model informed by blended rock attributes related to hardness is constructed, which is then integrated into
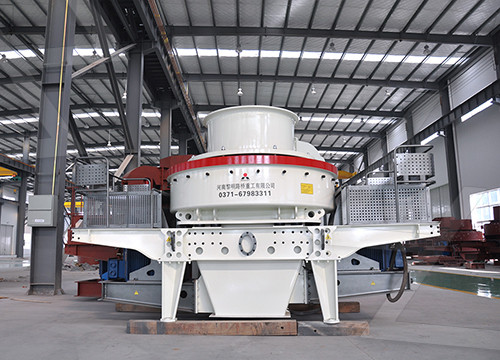
A Review of the Grinding Media in Ball Mills for Mineral
20231027 The ball mill is a rotating cylindrical vessel with grinding media inside, which is responsible for breaking the ore particles. Grinding media play an important role
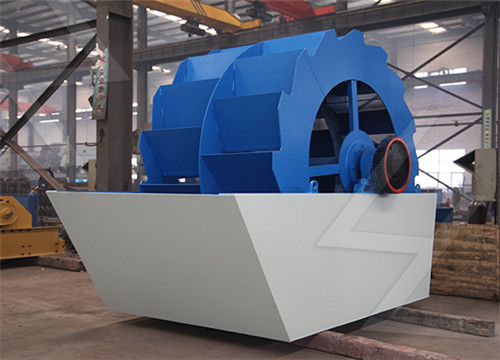
Ball Mill (Ball Mills Explained) saVRee saVRee
Ball mills are the most common grinding machine employed in the mining industry. Grinding occurs in a single stage, or multiple stages. Multiple stages may include a rod mill followed by a ball mill (two stage circuit), or
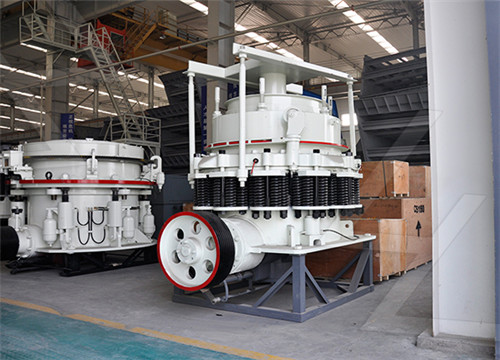
Addition of pebbles to a ball-mill to improve grinding
201741 The control of ball-mills is relatively simple in comparison (i.e. addition of balls to maintain power and control of the cyclones and pulp density). Pebble-milling is
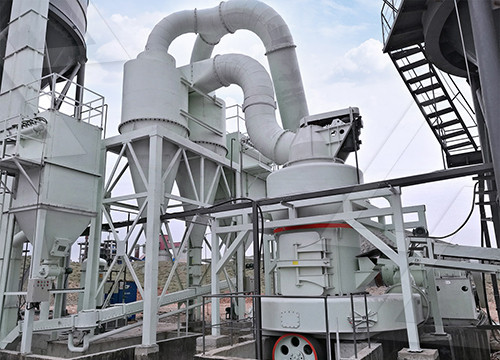
Helping to reduce mining industry carbon emissions: A step
2022330 Analysis of data on the performance of ball mills in HPGR circuits indicates that the “Morrell method” predicts circuit kWh/t to within 3%. Abstract. Comminution is a

Minerals Free Full-Text Optimizing Performance
2016122 The ball mill, the final grind stage, is closed with a hydrocyclone classifier that removes undersized material and sends it to the separation stage.
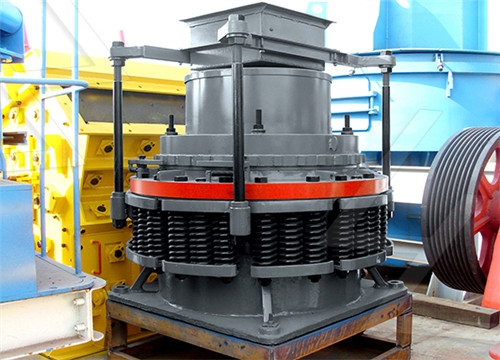
Energy Efficiency Analysis of Copper Ore Ball Mill
2021226 Abstract Milling is among the most energy-consuming technological stages of copper ore processing. It is performed in mills, which are machines of high rotational masses. The start of a mill filled to
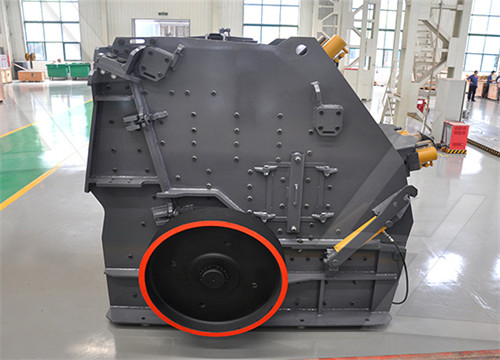
Machines Free Full-Text Modeling Impulsive Ball
2022323 This stone focuses on the vibration behavior of gearboxes driving ball mills in the mining industry, which often operate in a harsh environment due to shocks and collisions on the mill drum. Research has
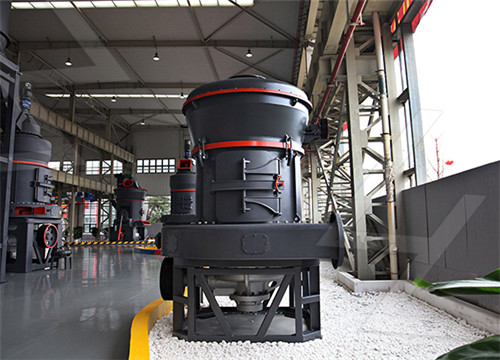
Ball Mill SpringerLink
2023430 Ball mill is a type of grinding equipment that uses the rotary cylinder to bring the grinding medium and materials to a certain height and make them squeeze,
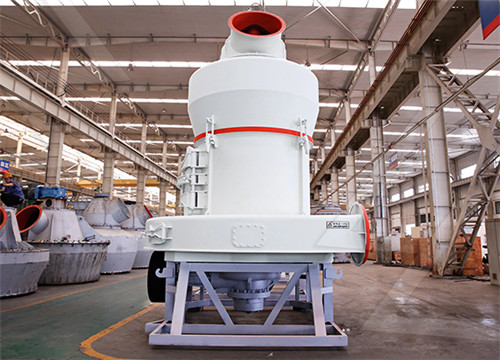
Integrating geometallurgical ball mill throughput predictions
202321 1. Introduction. Short-term mine production planning aims to make daily, weekly, or monthly operational decisions that best meet strategic production targets under existing operating conditions and constraints [1].Blom et al. [2] reviewed past advancements in short-term planning for open pit mines, while recent developments consider the
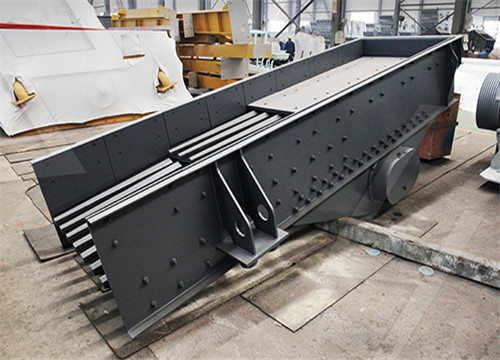
Ball Mill Ball Mills WetDry Grinding DOVE
2 DOVE small Ball Mills designed for laboratories ball milling process are supplied in 4 models, capacity range of (200g/h-1000 g/h). For small to large scale operations, DOVE Ball Mills are supplied in 17
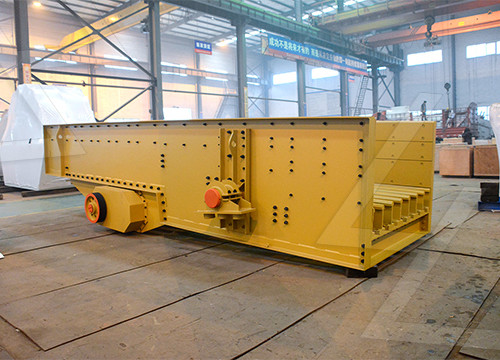
Physical Bauxite Processing: Crushing and Grinding of Bauxite
2022123 In this case the grinding circuit comprises an open circuit rod mill followed by a closed-circuit ball mill. The ball mill is most often closed over a classifier like a hydro cyclone (Fig. 3.11) or DSM style screen with a fine cut of 1–1.5 mm. The course material is returned to the ball mill feed and the fine screen underflow reports to the

Difference Between Sag Mill vs Ball Mill Mech4study
1. SAG mill is the primary tool for grinding. SAG mill is used before the other mills. Ball mill is a secondary, and it is used after the SAG mill. 2. SAG mill breaks the raw material into pieces for the further grinding. Ball mill is used to grind the pieces of raw material into. powder-like structures. 3.
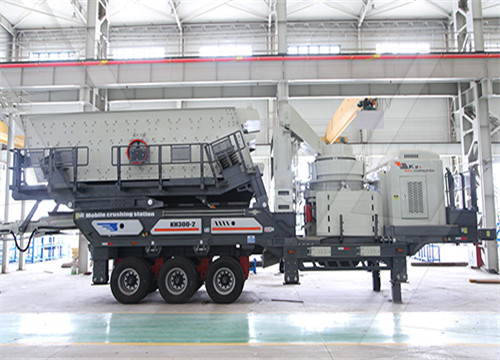
Tubular Ball Mills ScienceDirect
201611 A survey of 40 industrial mills in Australia found that the maximum ball mill diameter in use was 5.34 metres and length 8.84 metres [1]. Autogenous mills range up to 12 metres in diameter. The length-to-diameter ratios indicated in Table 7.1 for ball mills are for normal use, but for primary grinding the ratio could vary between 1:1 and 1.8:1
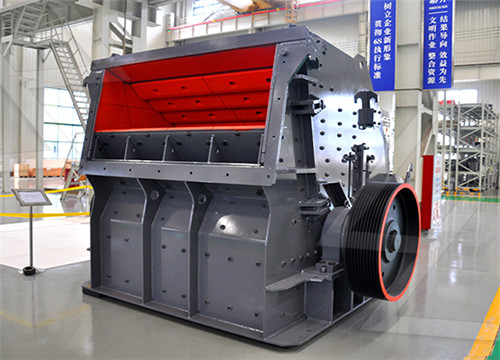
Energy Use of Fine Grinding in Mineral Processing SpringerLink
20131218 At Mt. Isa Mines, a GIS mill fed with material of F80 approximately 50 μm lowered the P80 size by only 5 to 10 μm, at the same time producing a large amount of fines. Similarly, in ball mills, it is known that grinding finer than approximately 40 μm will result in overgrinding of fines as well as high media consumption. However, it must be
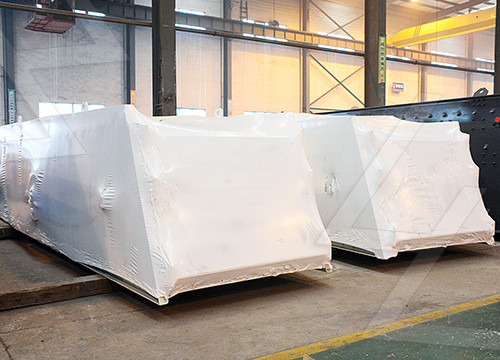
Consumption of steel grinding media in mills A review
201381 The dropped ball test (DBT) was originally developed by the US Bureau of Mines (Blickenderfer and Tylczak, 1983, Blickenderfer and Tylczak, 1985) and later adapted by the international Moly–Cop Grinding Systems organization to assess the resistance of any given sample or lot of balls to repeated severe ball-to-ball impacts. The DBT facility
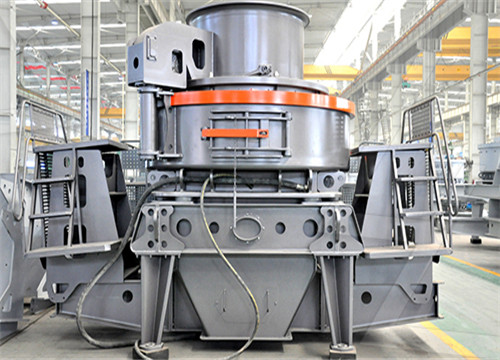
The Effect of Grinding Media on Mineral Breakage Properties
20211211 The breakage and liberation of minerals are the key to fluidized mining for minerals. In the ball milling process, steel balls function as not only a grinding action implementer but also energy carrier to determine the breakage behavior of ores and the production capacity of the mill. When ground products present a much coarse or much

How it Works: Crushers, Grinding Mills and
201762 Heavy mining, quarried materials, sandgravel, recycling: Gyratory crushers: Soft to very hard: Abrasive: Dry to slightly wet, not sticky: 4/1 to 7/1: Ball mills use a tumbling process with stone or metal balls

Grinding Mills Mineral Processing Equipment
20231012 To date, CITIC HIC has cumulatively produced and delivered over 1,550 mineral grinding mills, with a total installed power of 3,900MW. Our large-size grinding mills hold a market share of 85% in
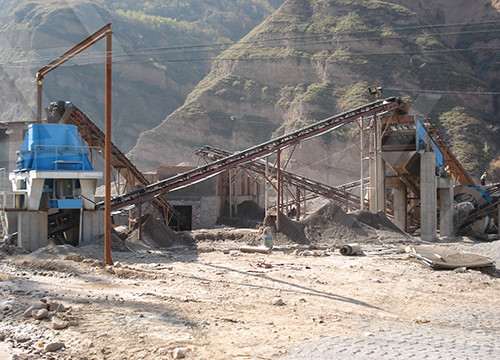
Grinding Balls and Other Grinding Media: Key consumables
2021125 Tower Mills: 0.5”-1.5” grinding balls are recommended. The normal top size of media used is 10-25mm, but even smaller grinding balls can be used for very fine grinding. Isa Mills: <0.1” grinding balls are recommended. The Isa Mill is more efficient when using small media (i.e. high-chrome steel balls).
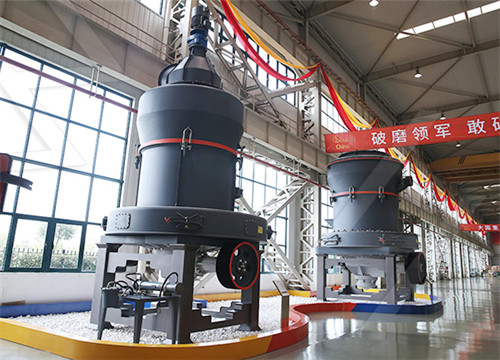
Grinding mills for mining and minerals processing Metso
Metso has over 100 years of experience in horizontal grinding mills and has always been an industry-leader in innovative technology. Metso's unmatched expertise ensures delivery of your Premier™ mill or Select™ mill based on your operational needs. When choosing your equipment we not only keep in mind mill performance, but also considering
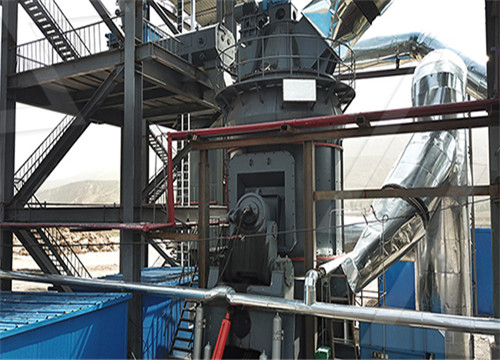
GMD system for Toromocho mine ABB
As a result, ABB developed three of the largest diameter and most powerful drive systems for a SAG and two ball mills installed at the highest altitude to date. The fully integrated and optimized solution for the grinding circuit consists of: 1 x 28 MW GMD to power the 40 ft SAG mill. 2 x 22 MW GMDs to power two 28 ft ball mills.
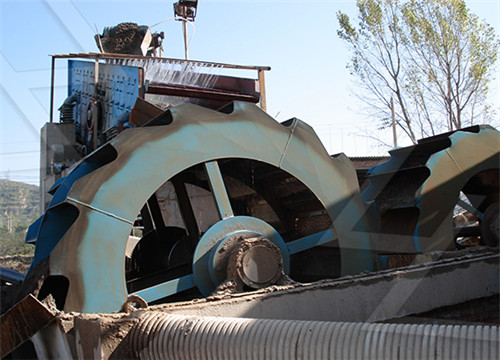
The Ultimate Guide to Ball Mills Mining-pedia
2019814 The Ultimate Guide to Ball Mills. Ball mill is a common grinding equipment in concentrator, the main role is to provide qualified grinding products for the subsequent dressing process. The ball grinding process is a process in which the steel ball rotates in the cylinder at a certain speed and rises with the wall of the cylinder.

(PDF) SIZE REDUCTION BY GRINDING METHODS
201734 Stamp mill ,Crusher,AG mill, SAG mill, Pebble m ill, Ball mill,Rod Crushing is the first step of mineral processing where the ore/rocks from the mine site is fed into the mechanical
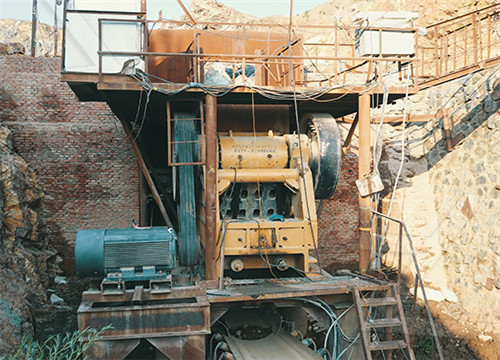
Bond Work Index an overview ScienceDirect Topics
The ability to simulate the Bond work index test also allows examination of truncated ball mill feed size distributions on the work index. For grinding circuits where the feed to a ball mill is sent directly to the classifier and the cyclone underflow feeds the ball mill (see Figure 3.10), a question arises as to whether this practice will alter the ball mill work index (BW i) of
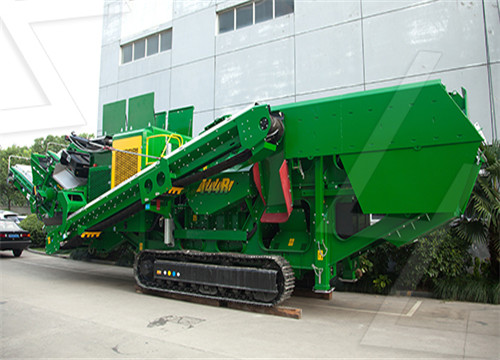
What’s the Difference Between SAG Mill and Ball Mill
20191126 The biggest characteristic of the sag mill is that the crushing ratio is large. The particle size of the materials to be ground is 300 ~ 400mm, sometimes even larger, and the minimum particle size of the materials to be discharged can reach 0.1 mm. The calculation shows that the crushing ratio can reach 3000 ~ 4000, while the ball mill’s

Ball Mill Balls Manufacturing Of High Quality Ball Mill Ball
Product Description. Ball mill balls are a type of ball used in ball mills, usually made of high-hardness materials such as steel, ceramics, hard alloys, etc. Ball mill steel balls is an important part of the ball mill, its main function is to carry out the grinding operation in the ball mill, and the material is crushed into the required size.
على الانترنت قائمة الأسعار الملح آلة سحق
يعمل كسارة الذهب
ثم كسارة إطلاق النار
الكسارة الدوارة سحق الجمعية رمح
مخطط خطي لعملية تصنيع الأسمنت
الصحافة حزام نزح المياه
موردي الحجر الأزرق
1000 عبتي الفحم محطم سحق
spect مزدوجة لفة محطم
الحزام الناقل المنهج
كسارة فكية متنقلة صغيرة في الصين
مطحنة الدرفلة الباردة Bmw
معدات لآلات تعدين الجرانيت
كسارات الخرسانة في لبنان الجديد لنا
افتتاح مصنعي الجهاز
سيمنز أجزاء من مخروط محطم شركة الحجر الجيري الابتدائي محطم
تستخدم موبيل محطم للبيع
لكسر المعادن بواسطة محطم عملية
تستخدم دولوميت كسارة سعر نيجيريا
طحن الكهربائي آلة الصانع
حجر تخطيط مخروط محطم
نماذج كسارة منجم للفحم ومعلمات
وجبة طحن التعدين
equipments use quarry
جيدًا حول تكلفة استثمار البوكسيت في
كسارة متنقلة ذات نوعية جيدة للبيع
حول لدينا
تأسست شركة Henan Lrate للعلوم والتكنولوجيا المحدودة التي تصنع معدات التكسير والطحن الكبيرة والمتوسطة الحجم في عام 1987. وهي شركة مساهمة حديثة مع البحث والتصنيع والمبيعات معًا.
على مدار أكثر من 30 عامًا ، تلتزم شركتنا بنظام الإدارة العلمية الحديث والتصنيع الدقيق والريادة والابتكار. الآن أصبحت LIMING رائدة في صناعة تصنيع الآلات المحلية والخارجية.