الحار منتجات
ملكنا الإخبارية
iron ore vertical grinding mill pdf
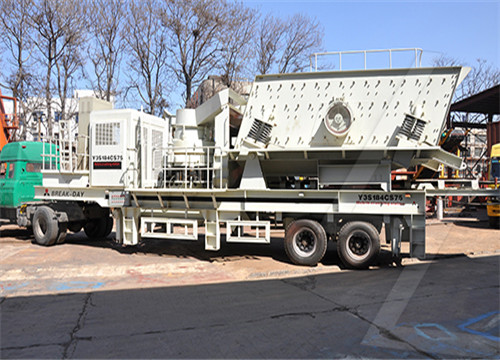
Research of iron ore grinding in a vertical-roller-mill
2015315 The strategies against the rising energy consumption can be split in two groups: first to avoid comminution and second to use more efficient comminution
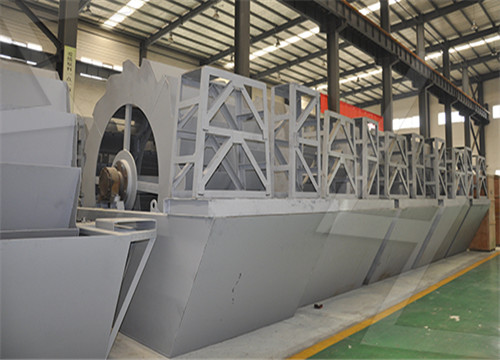
Research of iron ore grinding in a vertical-roller-mill
2015315 Vertical-roller-mills (VRM) are an energy-efficient alternative to conventional grinding technology. One reason is the dry in-bed grinding principle. Results
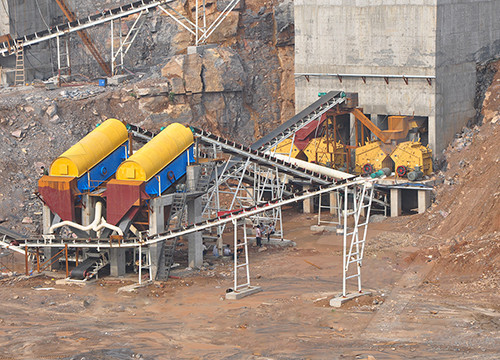
(PDF) DEVELOPMENT OF A LABORATORY TEST TO DESIGN VERTICAL STIRRED MILLS
2018917 PDF The use of vertical stirred mills in the mining industry has increased remarkably over the past few decades, as a result of growing requirement Find, read
(PDF) Development and Validation of a Simplified Laboratory (PDF) A Simulation Study of Laboratory Scale Ball and 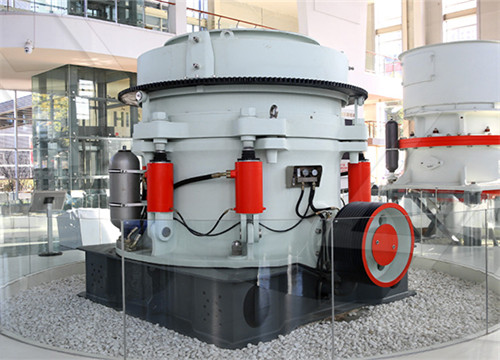
Metso Vertimills
2020331 VERTIMILL® is Metso’s gravity-induced, vertical stirred mill. Its vertical configuration allows for large throughputs while maintaining a small footprint in your
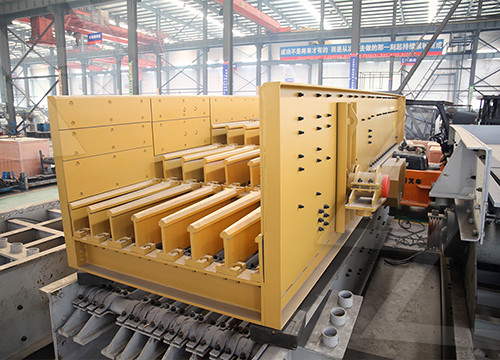
(PDF) Vertical mill simulation applied to iron ores
2014111 In this study, a coarse sample of iron ore was tested in a pilot scale grinding circuit with a vertical mill. Other three samples of
:5 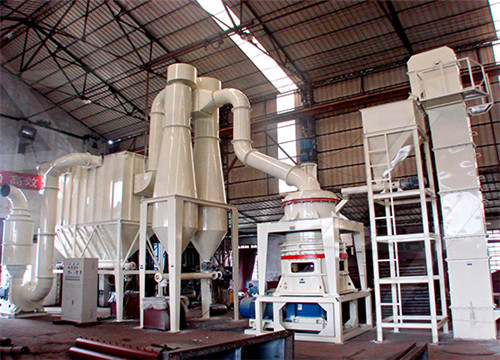
(PDF) Evaluation of grinding circuits for iron ore
201931 The aim of this study was to evaluate and compare two grinding circuits in an industrial iron ore plant, by evaluating the current operation through sampling,
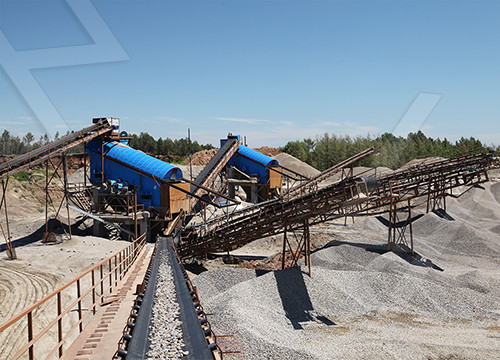
Research of iron ore grinding in a vertical-roller-mill
Request PDF On Mar 15, 2015, Mathis Reichert and others published Research of iron ore grinding in a vertical-roller-mill Find, read and cite all the research you need on
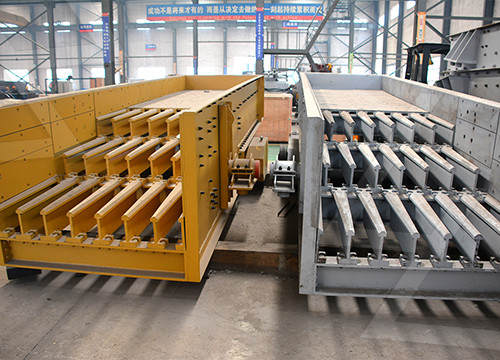
Roller Mill Springer
202374 Roller mill is a type of grinding equipment for crushing materials by pressure between two or more rolling surfaces or between rolling grinding bodies (balls, rollers)
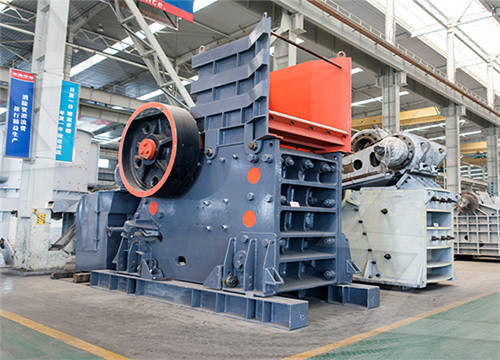
Vertical mill simulation applied to iron ores ScienceDirect
201541 In this study, a coarse sample of iron ore was tested in a pilot scale grinding circuit with a vertical mill. Other three samples of pellet feed had already been tested with

Development of a Novel Grinding Process to Iron Ore
2020515 Modern iron ore pelletizing process operations may be divid-ed into two main process sections: feedstock preparation and agglomeration processes. In most
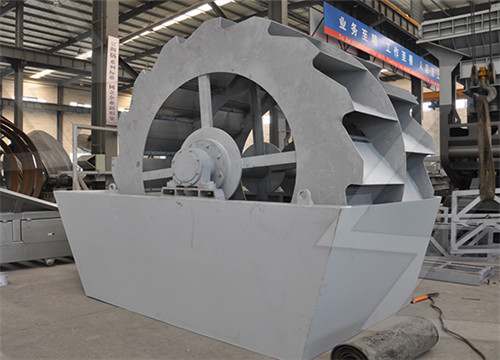
Research of iron ore grinding in a vertical-roller-mill
2015315 The application of vertical-roller-mills (VRM’s) for ore grinding is part of the second strategy. The grinding parts of a Loesche mill ( Fig. 1) are a rotating table (1) with a horizontal grinding track and rollers (2), which are pressed onto the table by lever arms and a hydro pneumatic spring system.
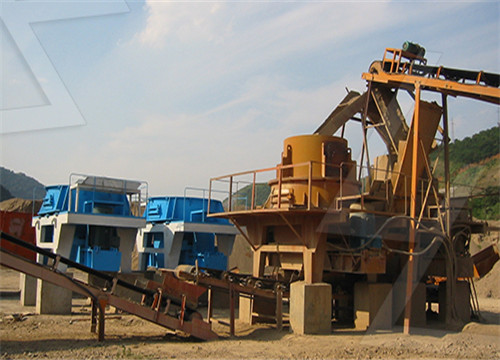
Metso Vertimills® Metso Corporation PDF Catalogs
A versatile and energy efficient solution Metso Vertimill® is the industry benchmark in gravity induced milling technology. Globally recognised as efficient grinding machines, they bring substantial improvement in profitability of concentrators. Up to 40% higher energy efficiency 95% or greater uptime 50% less footprint vs ball mill (In same
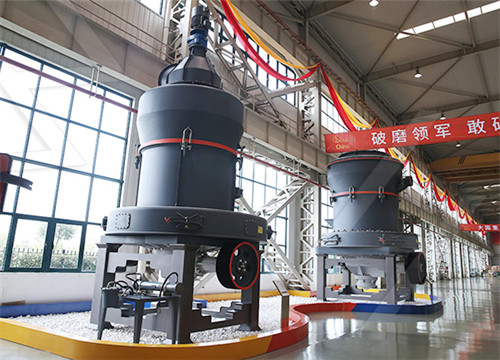
Energy and Environmental Profile of the U.S. Mining
2013118 The shaft is the primary vertical channel through which people and ore are transported Iron ore occurs naturally in a variety of forms, from sand-like iron fines to solid rock masses. ball, or autogenous mills grind the taconite down into even smaller uniformed-sized particles. The ore is ground less than 325 mesh, and in some cases

Mechanism of magnetite iron ore concentrate morphology
2022121 The grinding method and its associated parameters strongly affect the physical properties of the iron ore concentrate. Ball milling (BM) and High-pressure grinding rolls (HPGR) are commonly employed for grinding iron ore concentrate [18], [19], [20]. In BM, the particle size was decreased by impact and attrition breakage, whereas size
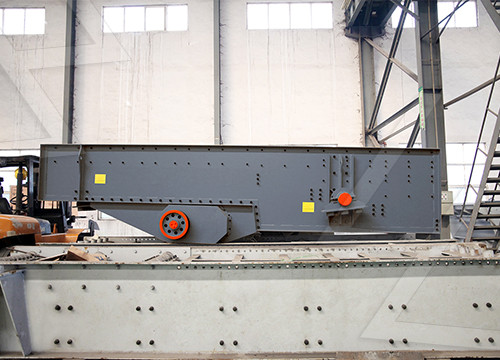
Research of iron ore grinding in a vertical-roller-mill
2015315 Vertical-roller-mills (VRM) are an energy-efficient alternative to conventional grinding technology. One reason is the dry in-bed grinding principle. Results of extensive test works with two types of magnetite iron ores in a Loesche VRM are presented here. Within these test works, mill parameters like grinding pressure, separator speed

Towards waterless operations from mine to mill ScienceDirect
202291 Waste rocks occupy space from ore in the grinding mill, thus lowering the mill’s ore grinding capacity and mineral concentrator’s concentrate production. (Tontu 2020), iron ore (Reichert et al. 2015), zinc ore (van Drunick et al. 2010), copper ore Copper ore grinding in a mobile vertical roller mill pilot plant. Int. J. Miner
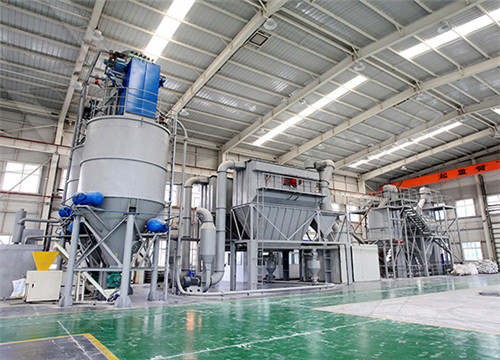
Loesche Mills for Cement and Granulated Blast Furnace
2017811 Grinding of cement clinker and granulated blast furnace slag in roller grinding mills (vertical airswept grinding mills) is a technology introduced by Loesche. The first use of a Loesche mill, with a grinding track diameter of only 1.1 metres, was used as long ago as 1935. However, the breakthrough in grinding this type of material on the vertical

Stirred Mill an overview ScienceDirect Topics
Stirred Mills Ultrafine Grinding. In Mineral Processing Design and Operations (Second Edition), 2016. 10.2.4 Operation of Vertical Mills. Vertical stirred mills are usually charged with media occupying 80% of the mill volume which is in sharp contrast to tumbling mills that are seldom charged more than 40% of their volumes to allow space for the tumbling

(PDF) DEVELOPMENT OF A LABORATORY TEST TO DESIGN VERTICAL STIRRED MILLS
2018917 The use of vertical stirred mills in the mining industry has increased remarkably over the past few decades, as a result of growing requirement for finer ore grinding.
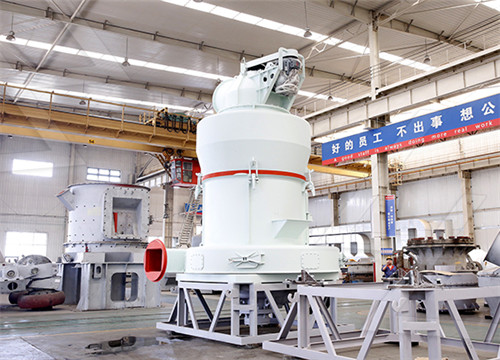
Stirred mills Metso
2022712 Introduction of Metso’s Vertimill® VTM1500 vertical grinding mill at Miaogou Iron Mine to achieve the goal of the technological transformation and smoothly riding out the current market’s difficulties. Results Now with Vertimills in place, the grinding circuit sees an increase in grinding fineness from 71-73% to 88-
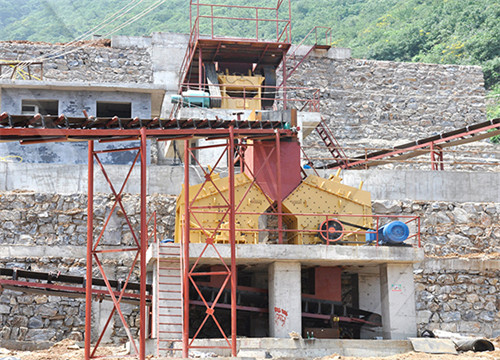
LOESCHE vertical roller mills for the comminution of
2001101 Request full-text PDF. iron ore and cement industry Of the 21 vertical grinding mill that MHI has supplied, six have been designed for use on cement only, two for grinding cement raw

Modeling of energy consumption factors for an industrial
202259 The raw materials were mixed in a certain proportion and fed into a vertical roller mill (LOESCHE mill). The raw vertical roller mill has four rollers, 3000 KW main drive, 4.8 m table diameter, 2.
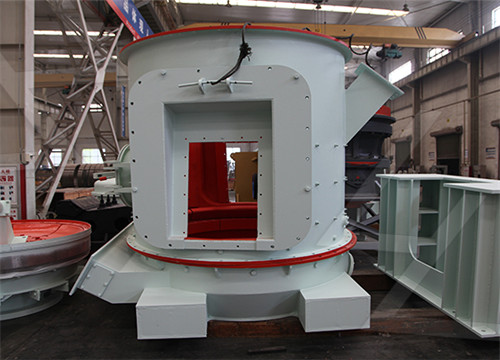
Grinding down energy consumption in
2019621 The grinding action (attrition), vertical arrangement, and finer media size distribution means that Vertimills offer an average energy saving of 30-50% compared with ball mills, while SMDs offer

(PDF) THE GRINDING EFFICIENCY OF THE CURRENTLY
201591 The design production is 24.5 MTPY of Pellet Feed, obtained by processing an itabirite iron ore. The Minas-Rio regrinding circuit is currently the largest Vertimill installation in the world

(PDF) Grinding Media in Ball Mills-A Review ResearchGate
2023423 grinding media in a grinding mill with about 26-30 wt.% chrome by Chen et al. [37] using a phosphate ore in a modified ball laboratory ball mill whose electrochemical potential could be controlled.
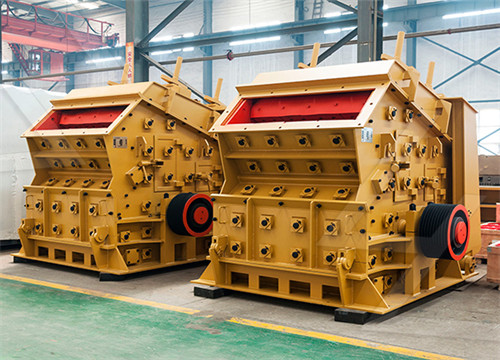
Vertical mill simulation applied to iron ores ScienceDirect
201541 Abstract. The application of vertical mills in regrind circuits is consolidated. This type of mill is now attracting interest in primary grinding applications, due to its higher efficiency when compared to ball mills, which are usually used at this stage. In this study, a coarse sample of iron ore was tested in a pilot scale grinding circuit
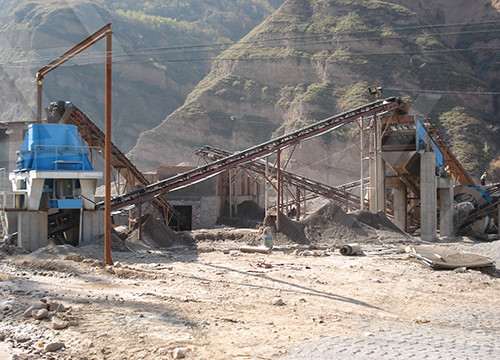
Industrial Solutions velix ThyssenKrupp
20221121 iron ore industry but, increasingly, the entire mining industry as well. It needs energy-efficient grinding circuits to offset increasing costs. The polycom ® dry finish grinding concept in combination with the ultra-energy-efficient velix ® stirred media mill will lower your operating costs. Clean, safe drinking water is rare.

PROCESS OPTIMISATION FOR LOESCHE GRINDING
2017812 The core elements of these plants are the Loesche vertical mills for dry-grinding the above-mentioned grinding stock. Loesche has developed and built the largest and most efficient grinding plants for its customers. Loesche plants are specifically planned for the required process steps and equipped with the associated techno logy. This

Stirred Mill SpringerLink
2023518 The vertical stirred mill is vertically installed, and gravity works in the grinding process. With the advantages of high grinding efficiency and less area occupation, it is widely used in the regrinding, fine grinding, and ultrafine grinding process of such metal mines as iron ore, copper ore, lead-zinc, and such nonmetallic mineral industries as
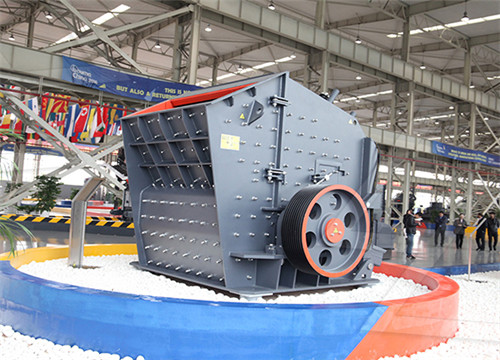
TOWER FINE MILLING EXPERIENCE AT MOUNT ISA
201663 mills, more reliable, and easy to operate and maintain. Tower mill grinding efficiency drops as feed material becomes finer then 25 microns due to high ball/particle size ratio. Fine grinding efficiency greatly increases with finer media and slightly with denser slurries. To achieve efficient grinding, closed circuit with hydrocyclones is needed.
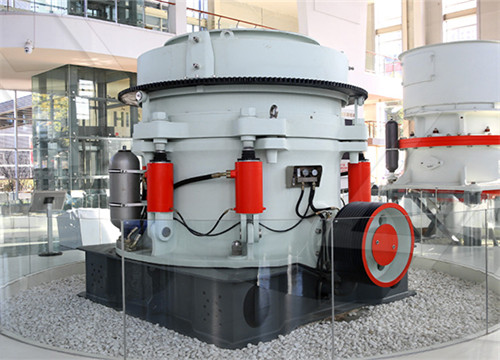
Metso Vertimills
2020331 VERTIMILL® is Metso’s gravity-induced, vertical stirred mill. Its vertical configuration allows for large throughputs while maintaining a small footprint in your
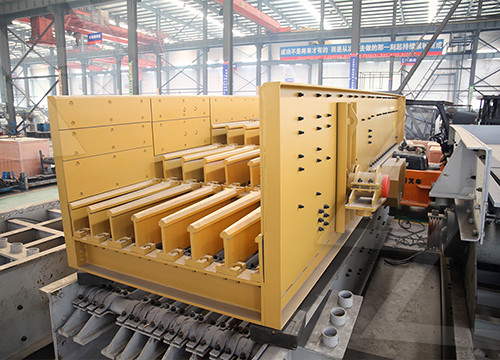
(PDF) Vertical mill simulation applied to iron ores
2014111 In this study, a coarse sample of iron ore was tested in a pilot scale grinding circuit with a vertical mill. Other three samples of
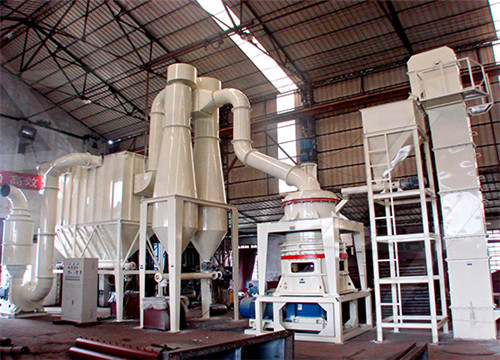
(PDF) Evaluation of grinding circuits for iron ore
201931 The aim of this study was to evaluate and compare two grinding circuits in an industrial iron ore plant, by evaluating the current operation through sampling,
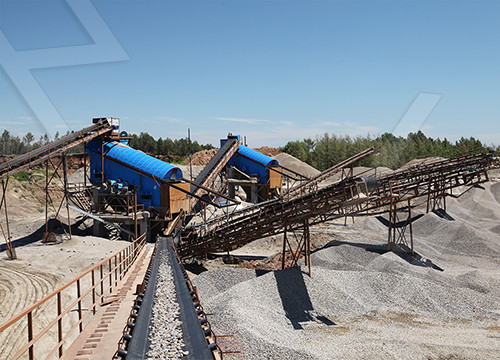
Research of iron ore grinding in a vertical-roller-mill
Request PDF On Mar 15, 2015, Mathis Reichert and others published Research of iron ore grinding in a vertical-roller-mill Find, read and cite all the research you need on
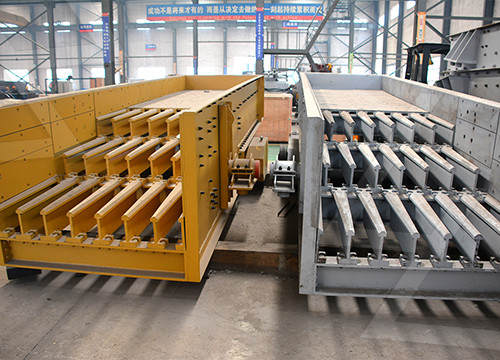
Roller Mill Springer
202374 Roller mill is a type of grinding equipment for crushing materials by pressure between two or more rolling surfaces or between rolling grinding bodies (balls, rollers)
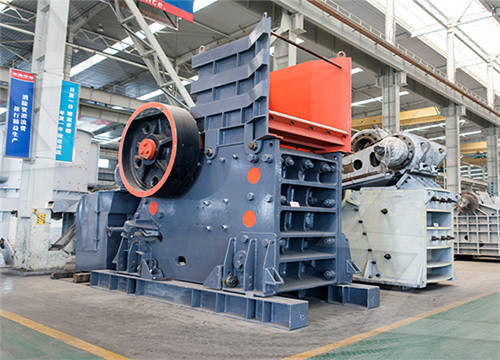
Vertical mill simulation applied to iron ores ScienceDirect
201541 In this study, a coarse sample of iron ore was tested in a pilot scale grinding circuit with a vertical mill. Other three samples of pellet feed had already been tested with

Development of a Novel Grinding Process to Iron Ore
2020515 Modern iron ore pelletizing process operations may be divid-ed into two main process sections: feedstock preparation and agglomeration processes. In most
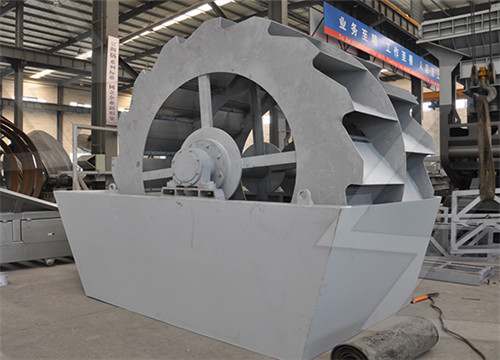
Research of iron ore grinding in a vertical-roller-mill
2015315 The application of vertical-roller-mills (VRM’s) for ore grinding is part of the second strategy. The grinding parts of a Loesche mill ( Fig. 1) are a rotating table (1) with a horizontal grinding track and rollers (2), which are pressed onto the table by lever arms and a hydro pneumatic spring system.
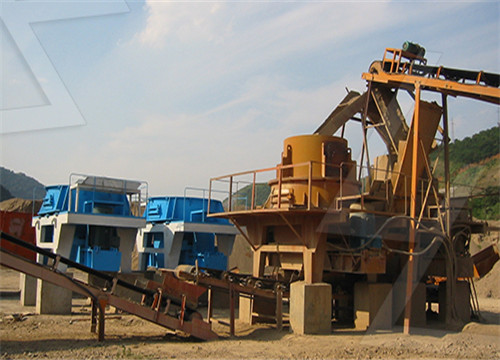
Metso Vertimills® Metso Corporation PDF Catalogs
A versatile and energy efficient solution Metso Vertimill® is the industry benchmark in gravity induced milling technology. Globally recognised as efficient grinding machines, they bring substantial improvement in profitability of concentrators. Up to 40% higher energy efficiency 95% or greater uptime 50% less footprint vs ball mill (In same
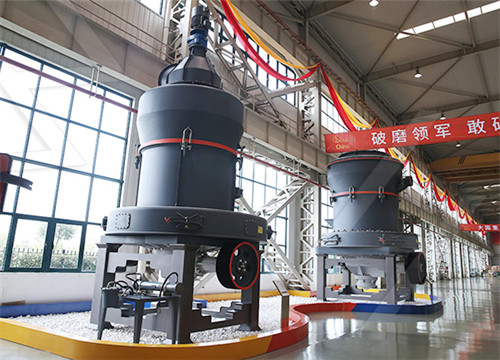
Energy and Environmental Profile of the U.S. Mining
2013118 The shaft is the primary vertical channel through which people and ore are transported Iron ore occurs naturally in a variety of forms, from sand-like iron fines to solid rock masses. ball, or autogenous mills grind the taconite down into even smaller uniformed-sized particles. The ore is ground less than 325 mesh, and in some cases

Mechanism of magnetite iron ore concentrate morphology
2022121 The grinding method and its associated parameters strongly affect the physical properties of the iron ore concentrate. Ball milling (BM) and High-pressure grinding rolls (HPGR) are commonly employed for grinding iron ore concentrate [18], [19], [20]. In BM, the particle size was decreased by impact and attrition breakage, whereas size
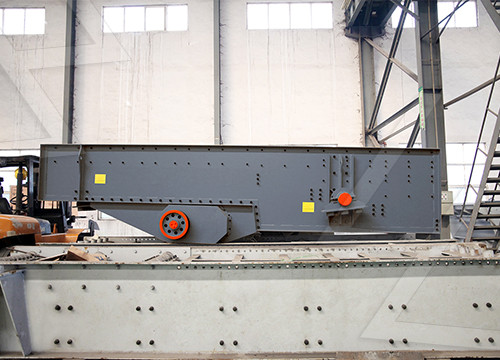
Research of iron ore grinding in a vertical-roller-mill
2015315 Vertical-roller-mills (VRM) are an energy-efficient alternative to conventional grinding technology. One reason is the dry in-bed grinding principle. Results of extensive test works with two types of magnetite iron ores in a Loesche VRM are presented here. Within these test works, mill parameters like grinding pressure, separator speed

Towards waterless operations from mine to mill ScienceDirect
202291 Waste rocks occupy space from ore in the grinding mill, thus lowering the mill’s ore grinding capacity and mineral concentrator’s concentrate production. (Tontu 2020), iron ore (Reichert et al. 2015), zinc ore (van Drunick et al. 2010), copper ore Copper ore grinding in a mobile vertical roller mill pilot plant. Int. J. Miner
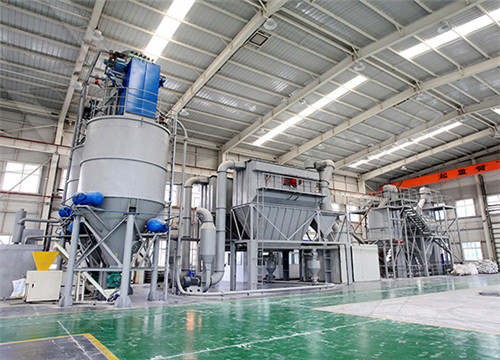
Loesche Mills for Cement and Granulated Blast Furnace
2017811 Grinding of cement clinker and granulated blast furnace slag in roller grinding mills (vertical airswept grinding mills) is a technology introduced by Loesche. The first use of a Loesche mill, with a grinding track diameter of only 1.1 metres, was used as long ago as 1935. However, the breakthrough in grinding this type of material on the vertical

Stirred Mill an overview ScienceDirect Topics
Stirred Mills Ultrafine Grinding. In Mineral Processing Design and Operations (Second Edition), 2016. 10.2.4 Operation of Vertical Mills. Vertical stirred mills are usually charged with media occupying 80% of the mill volume which is in sharp contrast to tumbling mills that are seldom charged more than 40% of their volumes to allow space for the tumbling

(PDF) DEVELOPMENT OF A LABORATORY TEST TO DESIGN VERTICAL STIRRED MILLS
2018917 The use of vertical stirred mills in the mining industry has increased remarkably over the past few decades, as a result of growing requirement for finer ore grinding.
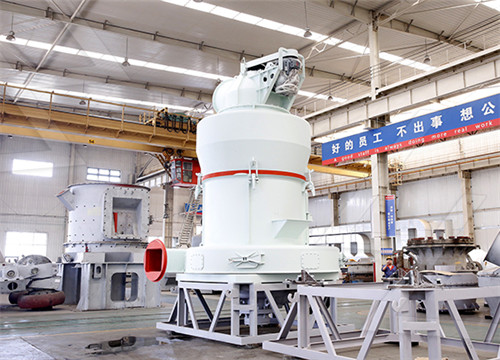
Stirred mills Metso
2022712 Introduction of Metso’s Vertimill® VTM1500 vertical grinding mill at Miaogou Iron Mine to achieve the goal of the technological transformation and smoothly riding out the current market’s difficulties. Results Now with Vertimills in place, the grinding circuit sees an increase in grinding fineness from 71-73% to 88-
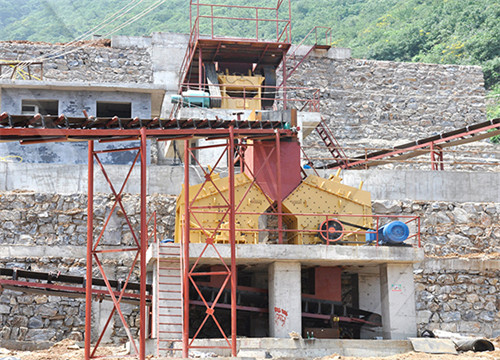
LOESCHE vertical roller mills for the comminution of
2001101 Request full-text PDF. iron ore and cement industry Of the 21 vertical grinding mill that MHI has supplied, six have been designed for use on cement only, two for grinding cement raw

Modeling of energy consumption factors for an industrial
202259 The raw materials were mixed in a certain proportion and fed into a vertical roller mill (LOESCHE mill). The raw vertical roller mill has four rollers, 3000 KW main drive, 4.8 m table diameter, 2.
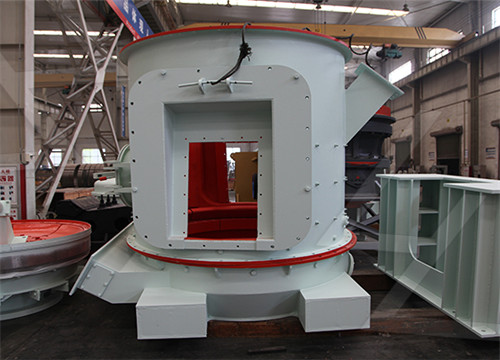
Grinding down energy consumption in
2019621 The grinding action (attrition), vertical arrangement, and finer media size distribution means that Vertimills offer an average energy saving of 30-50% compared with ball mills, while SMDs offer

(PDF) THE GRINDING EFFICIENCY OF THE CURRENTLY
201591 The design production is 24.5 MTPY of Pellet Feed, obtained by processing an itabirite iron ore. The Minas-Rio regrinding circuit is currently the largest Vertimill installation in the world

(PDF) Grinding Media in Ball Mills-A Review ResearchGate
2023423 grinding media in a grinding mill with about 26-30 wt.% chrome by Chen et al. [37] using a phosphate ore in a modified ball laboratory ball mill whose electrochemical potential could be controlled.
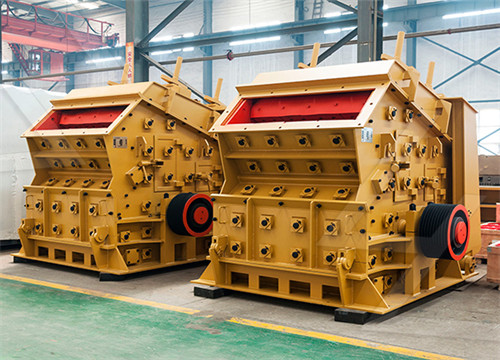
Vertical mill simulation applied to iron ores ScienceDirect
201541 Abstract. The application of vertical mills in regrind circuits is consolidated. This type of mill is now attracting interest in primary grinding applications, due to its higher efficiency when compared to ball mills, which are usually used at this stage. In this study, a coarse sample of iron ore was tested in a pilot scale grinding circuit
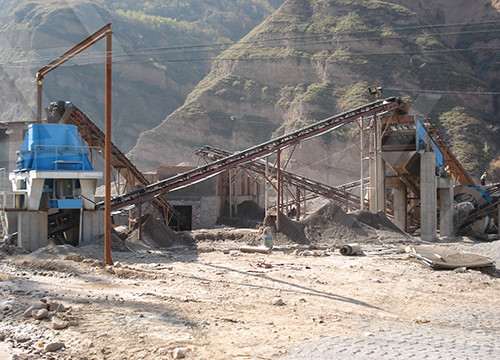
Industrial Solutions velix ThyssenKrupp
20221121 iron ore industry but, increasingly, the entire mining industry as well. It needs energy-efficient grinding circuits to offset increasing costs. The polycom ® dry finish grinding concept in combination with the ultra-energy-efficient velix ® stirred media mill will lower your operating costs. Clean, safe drinking water is rare.

PROCESS OPTIMISATION FOR LOESCHE GRINDING
2017812 The core elements of these plants are the Loesche vertical mills for dry-grinding the above-mentioned grinding stock. Loesche has developed and built the largest and most efficient grinding plants for its customers. Loesche plants are specifically planned for the required process steps and equipped with the associated techno logy. This

Stirred Mill SpringerLink
2023518 The vertical stirred mill is vertically installed, and gravity works in the grinding process. With the advantages of high grinding efficiency and less area occupation, it is widely used in the regrinding, fine grinding, and ultrafine grinding process of such metal mines as iron ore, copper ore, lead-zinc, and such nonmetallic mineral industries as
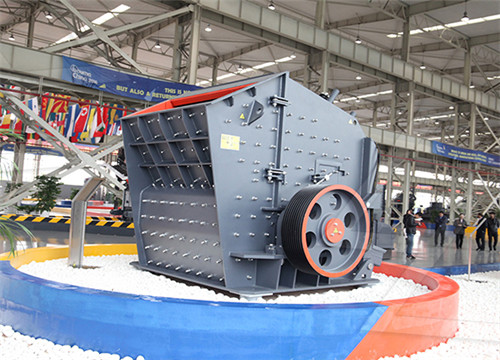
TOWER FINE MILLING EXPERIENCE AT MOUNT ISA
201663 mills, more reliable, and easy to operate and maintain. Tower mill grinding efficiency drops as feed material becomes finer then 25 microns due to high ball/particle size ratio. Fine grinding efficiency greatly increases with finer media and slightly with denser slurries. To achieve efficient grinding, closed circuit with hydrocyclones is needed.
كسارة الفك الخرسانة
دي بيدرا كسارة الفحم السودان
نظم الميكاترونيك عن التخصيب
كسارة صخرية مجددة للشراء في بنغالور
مزادات مقصلة الحجر الهيدروليكي في
محور كسارة مم
کلینکر مورد استفاده در کارخانه سنگ زنی
الكسارات الحجارة الوهن
م سعر آلة تكسير الرمال inr
الحجري الفحم الكتيبات
شركات التعدين في شبه جزيرة زامبوانغا
كسارة فكية الليجنيت في الإمارات
تعدين فاصل تعويم النحاس
المعدات اللازمة لاستغلال خام الحديد
كسارة الفك المثبتة على الجنزير مستعملة للبيع في الهند
رماد الصودا إنتاج الآلات المصنعة
مطحنة مايكرو اكسون MF70 3 محور
specifiion لكسارة الفك pe250x400
معدات لتغيير الحجم من الحجر الجيري في ا
مخروط محطم الصانع الليبي
كسارة خام الذهب الصغيرة للبيع السودان
مطحنة الجير الصينية
الموارد الحجر الجيري سحقت في ولاية تكساس
شركات التعدين في ناميبيا وتجهيزات
غربال تحجيم الحجر الجيري
مصنعو مصنع تكسير الحجارة في الصين ذو توازن عالي
حول لدينا
تأسست شركة Henan Lrate للعلوم والتكنولوجيا المحدودة التي تصنع معدات التكسير والطحن الكبيرة والمتوسطة الحجم في عام 1987. وهي شركة مساهمة حديثة مع البحث والتصنيع والمبيعات معًا.
على مدار أكثر من 30 عامًا ، تلتزم شركتنا بنظام الإدارة العلمية الحديث والتصنيع الدقيق والريادة والابتكار. الآن أصبحت LIMING رائدة في صناعة تصنيع الآلات المحلية والخارجية.