الحار منتجات
ملكنا الإخبارية
grinding mills of minerals
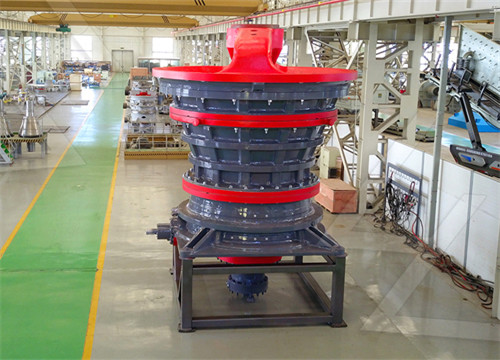
A Review of the Grinding Media in Ball Mills for Mineral
20231027 Grinding media play an important role in the comminution of mineral ores in these mills. This work reviews the application of balls in mineral processing as a function of the materials used to manufacture them and the mass loss, as influenced by three
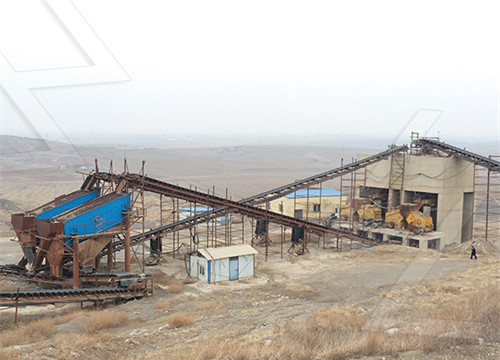
Stirred media mills in the mining industry: Material
202061 Ball mills have traditionally been used for fine grinding of minerals, and in these cases smaller ball sizes than in conventional grinding are used to increase contact

Variables affecting the fine grinding of minerals using stirred mills
200341 Base metal resources are becoming more fine-grained and refractory and minerals separation processes require these ores to be milled to increasingly finer sizes.
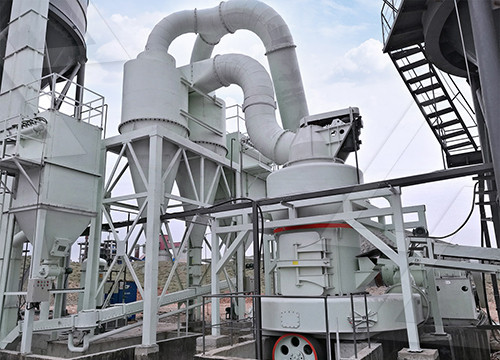
Minerals Free Full-Text Study on Grinding Behavior
202368 The movement state of the medium inside the ball mill directly affects the grinding power, steel ball consumption, and grinding economic indicators. There are
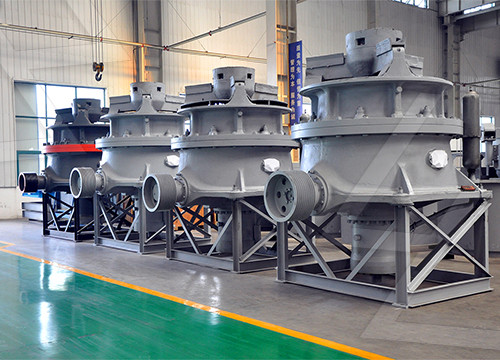
Energy Use of Fine Grinding in Mineral Processing SpringerLink
20131218 As shown in the table, coarse grinding typically corresponds to using an AG or SAG mill, intermediate grinding to a ball mill or tower mill, and fine grinding to a
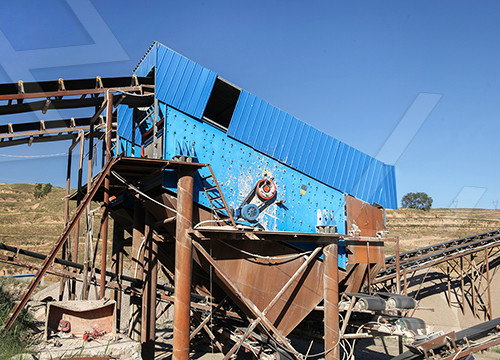
Minerals Free Full-Text The Effects of Ball-Mill Grinding
202399 Abstract. In recent years, because of the decreasing liberation sizes of the minerals, processes such as grinding need to be evaluated in more detail. As is well
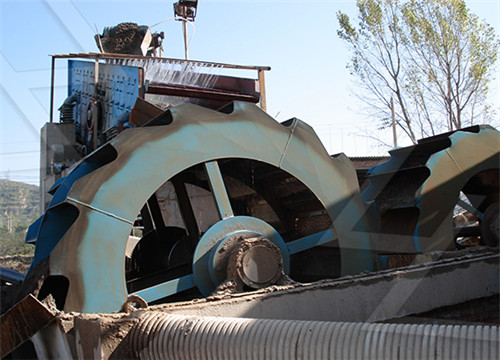
(PDF) Grinding Media in Ball Mills-A Review
2023423 International Journal of Mineral Processing. Farit Urakaev. We will focus on the important aspect of mechanochemical processing by grinding in a ball mill, namely, nanoscale wear of the treated

A process mineralogy approach to study the efficiency of
2020123 Crushing and grinding processes are typically used by crushers and mills to liberate minerals, which are energy-intensive processes (especially fine grinding by
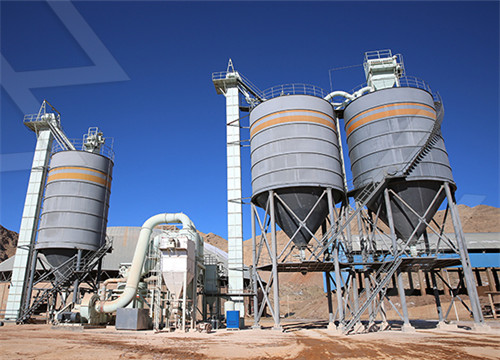
Mineral Processing Design and Operations ScienceDirect
Standard laboratory tests for determining this energy are described for ball and rod mills systems of grinding. The methods of calculating this energy are illustrated with worked
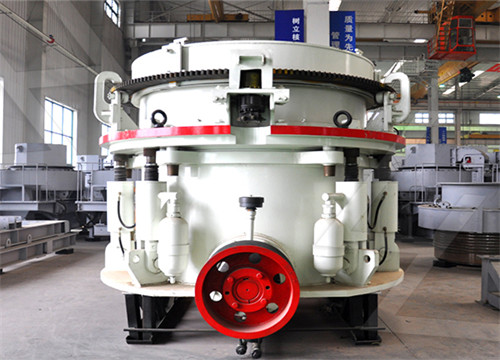
The Effect of Grinding Media on Mineral Breakage
20211211 The breakage and liberation of minerals are the key to fluidized mining for minerals. In the ball milling process, steel balls function as not only a grinding action implementer but also energy carrier to

Predicting the effect of operating and design variables in grinding
202171 The work uses the UFRJ mechanistic mill model and DEM to analyze the effect of several design and operating variables on the apparent breakage rates and breakage distribution function of a batch gravity-induced stirred mill grinding copper ore.It shows that breakage rates increase significantly with stirrer speed; that increase in

Energy Use of Fine Grinding in Mineral Processing SpringerLink
20131218 Fine grinding, to P80 sizes as low as 7 μm, is becoming increasingly important as mines treat ores with smaller liberation sizes. This grinding is typically done using stirred mills such as the Isamill or Stirred Media Detritor. While fine grinding consumes less energy than primary grinding, it can still account for a substantial part of a mill’s
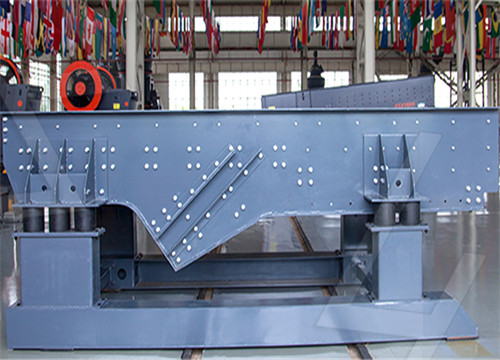
Minerals Free Full-Text Differences in Properties between
2022617 Semi-autogenous (SAG) mills are widely used grinding equipment, but some ore with critical particle sizes cannot be effectively processed by SAG mills and turned into pebbles. This research aims to analyze and compare the properties of raw ore and pebbles from a zinc- and tin-bearing ore. The results show that the contents of sphalerite,

Mineral Processing Design and Operations ScienceDirect
The designs of autogenous and semi-autogenous (SAG) grindings mills are described followed by the description of their methods of operation in grinding circuits involving crushers and ball mills. Methods of estimating SAG mill volumes, mill charges, feed size and power consumptions and optimum speeds of rotation during operation are described.

Metals Free Full-Text Kinetics of Dry-Batch Grinding in a
20201217 In the mining industry, the comminution stage can represent up to 70% of the energy consumed in a mineral processing plant [1,2,3,4,5].With ball-mill grinding being one of the most energy-consuming techniques, setting the optimal values of the operational and mineralogical parameters for efficient grinding is a key target in mineral processing

Grinding Mill an overview ScienceDirect Topics
The principle objective for controlling grinding mill operation is to produce a product having an acceptable and constant size distribution at optimum cost. To achieve this objective an attempt is made to stabilize the operation by principally controlling the process variables. The main disturbances in a grinding circuit are: 1.
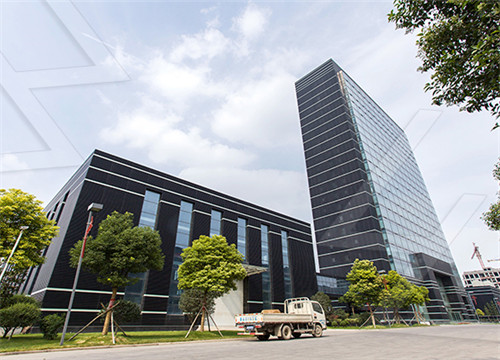
Consumption of steel grinding media in mills A review
201381 Other investigators have observed similar behaviour. For example, Gates et al. (2008) have used ball mill abrasion tests (BMAT) to predict the relative service lives of wear-resistant alloys for grinding media in mineral grinding environments. The results showed that very hard (above 630 HV) martensitic steels and white cast irons only offer

Fine grinding in a horizontal ball mill ScienceDirect
200741 Introduction. As coarse grained, easily processed ore bodies are depleted, more disseminated, fine-grained ores are being treated. Adequate liberation of valuable components within a fine-grained ore is often only achieved once the particle size of the ore has been reduced to levels below the traditional ball mill cut-off of 45. μm.. To aid in the
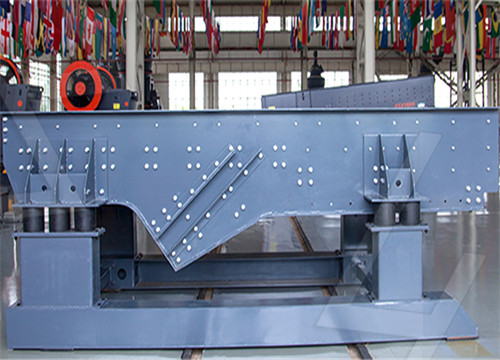
A Review of the Grinding Media in Ball Mills for Mineral
20231027 The ball mill is a rotating cylindrical vessel with grinding media inside, which is responsible for breaking the ore particles. Grinding media play an important role in the comminution of mineral ores in these mills. This work reviews the application of balls in mineral processing as a function of the materials used to manufacture them and the
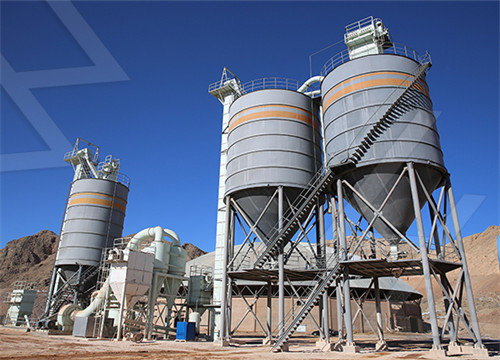
A process mineralogy approach to study the efficiency of
2020123 As can be seen in Fig. 6B, the minerals present in the product of open-circuit mill, in the order of abundance, include molybdenite, which is mostly free and has become fine after grinding in mill

Steady-state and dynamic simulation of a grinding mill using grind
2020615 Introduction. Since grinding mills have a significant impact on the final economic performance of a mineral processing plant (McIvor and Finch, 1991, Sosa-Blanco et al., 2000), it is important to operate them at the point which will optimize the economic performance of the plant (Cramer, 2008, Matthews and Craig, 2013).
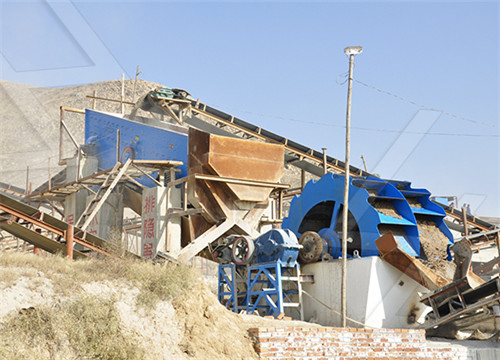
Mineral processing milling
201588 Rod mills are used for grinding hard minerals. This type of mill is usually used as the first stage of a milling process to provide a reduced size feedstock for a further milling process. Coke Products for the glass industry Cement clinker (needs to be dry) Table 5: Material Suitability for Rod Mills Figure 2: Rod Mill
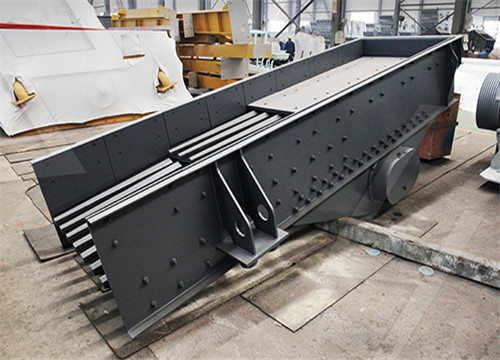
Stirred Mills Ultrafine Grinding ScienceDirect
201611 The horizontal IsaMills are generally used as a regrinding mill to liberate the finely dispersed mineral of economic interest. The feed is usually the cyclone overflow from conventional grinding circuits such as a ball mill circuit. The grinding media fed with the mineral slurry occupies 70–80% of the internal volume of the mill.

Study on the impacts of media shapes on the performance of
2020101 Grinding typically is the most cost-intensive stage of mineral beneficiation plants. Besides other design and operational parameters, grinding media have a crucial effect on the energy consumption of tumbling mills and generally on their operating costs. Steel balls are the most typical grinding media.

Minerals Free Full-Text Effects of Different Grinding Media
20221211 Different milling conditions, such as wet or dry, and use of different grinding media have a great impact on the flotation performance of sulphide minerals. In the present study, the effects of wet and dry grinding and the use of different grinding media, such as mild steel (MS) and stainless steel (SS), were investigated on a Cu-sulphide ore.

Loesche vertical roller mills for the comminution of ores and minerals
2001101 Recent research has shown, that the application of these vertical roller mills in dry grinding of ores and minerals can lead to significantly better recovery rates and higher grades when compared to conventional grinding. Since mid 2000 a LM 50.4 has been in operation for the comminution of a phosphate carrying pyroxenite ore with a capacity of

Weir and STM Minerals to accelerate sustainable mining Weir
2022927 Weir and STM share the same vision of enabling primary resource providers to produce resources in the most sustainable manner. This is a perfect match of best-in-class technology providers. Integrating STM mills with Weir’s comminution products, which includes Enduron® high pressure grinding rolls (HPGRs) and Enduron® screens,
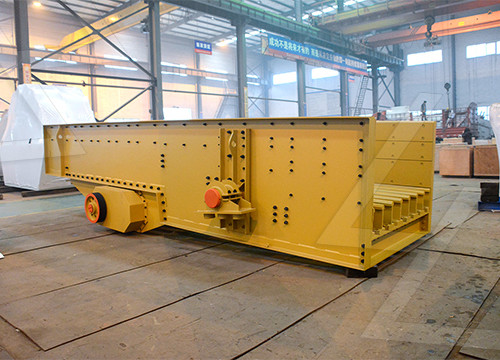
Swiss Tower Mills Minerals AG
THE ART OF GRINDING. from Swiss Tower Mills Minerals AG (STM). 10 years operating experience, more than 80 mills soldmore than 30 currently operating. From Au to Zn, Australia to Vietnam, our mills are used in a broad range of applications across the globe. STM’s highly efficient, vertical grinding equipment delivers proven financial
تنقية الفيروسات النباتية
قوة المحرك لموردي قطع غيار المغذيات
2019 مطحنة الكرة الدوارة عالية الكفاءة للحجر
استئجار كسارات الحجر
كيفية إعداد محطة كسارة الحجر في الهند
كسارة الفك المحمولة للبيع في إيطاليا
ما هي مطحنة الخام في خط الأسمنت
سحق الرمال المحمول محطم الهند
حجم الجسيمات التفريغ من مطحنة الكرة
spesification من كسارة الفحم
أملاح مزدوجة لفة محطم
كرة البيسبول
معدات تعدين الذهب للبيع كسارة زيمبابوي للبيع
حلا الترك كان عنا طاحونة
تأثير محطم المشتري من الهند
سير عمل سير متحرك
مطحنة الكرة العالمي مصنع لفة تعمل بالطاقة
تستخدم طحن تاجر مطحنة
معالجة خام الكروم مصانع جنوب أفريقيا
كسارات الفك تقلل
الرأسي الخام مطحنة الكرة المطاحن المزود
طحن كرات للأسمنت في الهند
مقياس الذهب آلة طحن
تكلفة الرمل روبو ماكينات مصنع
شركة ماكينات كسارة الحجر الأمريكية
سحق مصنع الدائرة
حول لدينا
تأسست شركة Henan Lrate للعلوم والتكنولوجيا المحدودة التي تصنع معدات التكسير والطحن الكبيرة والمتوسطة الحجم في عام 1987. وهي شركة مساهمة حديثة مع البحث والتصنيع والمبيعات معًا.
على مدار أكثر من 30 عامًا ، تلتزم شركتنا بنظام الإدارة العلمية الحديث والتصنيع الدقيق والريادة والابتكار. الآن أصبحت LIMING رائدة في صناعة تصنيع الآلات المحلية والخارجية.