الحار منتجات
ملكنا الإخبارية
information on ball mill for grinding gold ore
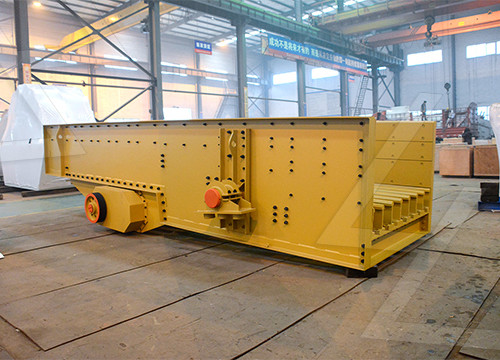
A Review of the Grinding Media in Ball Mills for Mineral
20231027 The ball mill is a rotating cylindrical vessel with grinding media inside, which is responsible for breaking the ore particles. Grinding media play an important role in the comminution of mineral ores in these mills. This work reviews the application of balls
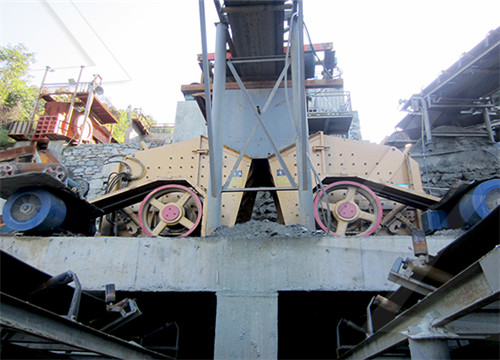
Comminution circuits for gold ore processing ScienceDirect
200511 Introduction For the vast majority of ounces of gold produced, comminution costs in the form of power, grinding media, and liners represent the single largest cost

How to Process Gold Ore? 4 Gold Processing Steps Mining
Method #1: Gold Cyanidation ProcessMethod #2: Gold Flotation ProcessMethod #3: Gold Gravity Separation ProcessMethod #1: Tailings ReprocessingMethod #2: Tailings Dry StackingMethod #3: Tailings Filling Goaf
The cyanidation process is one of the main methods of extracting gold from ore. The gold cyanidation process can be divided into agitation cyanidation and percolation cyanidation. The agitation cyanidation process is used to process tailings after gravity separation, amalgamation and flotation of gold-containing concentrates, or for all-sliming cya...
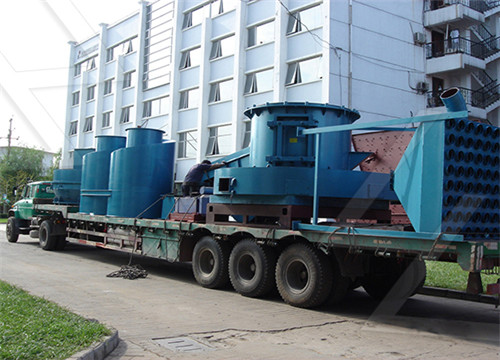
What is a ball mill used for in gold mining? LinkedIn
202369 A ball mill is a grinding machine used to grind, blend, and sometimes for mixing materials for use in the process of extracting gold from ores in gold mining
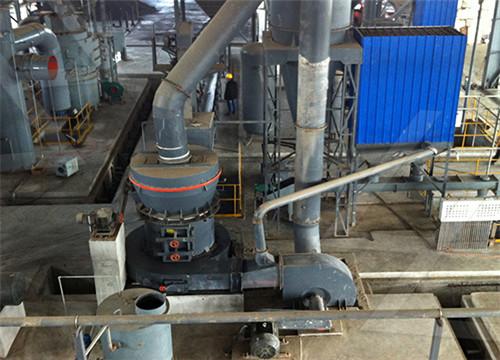
Ball Mill Mining Grinding Mill Mineral Processing
1 Common ones include grinding gold, copper, iron ore, molybdenum ore, feldspar ore, lithium, chrome, fluorite ore, etc. Types: Mining ball
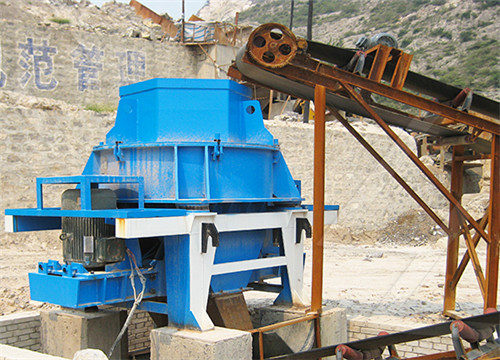
Comminution Circuits for Gold Ore Processing ScienceDirect
201611 1. Introduction For the vast majority of ounces of gold produced, comminution costs in the form of power, grinding media, and liners represent the single
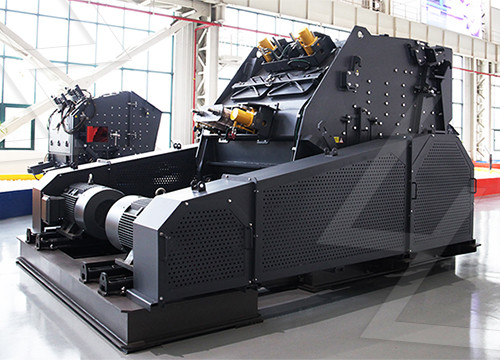
The Effect of Grinding Media on Mineral Breakage
20211211 Abstract. The breakage and liberation of minerals are the key to fluidized mining for minerals. In the ball milling process, steel balls function as not only a grinding action implementer but also energy carrier
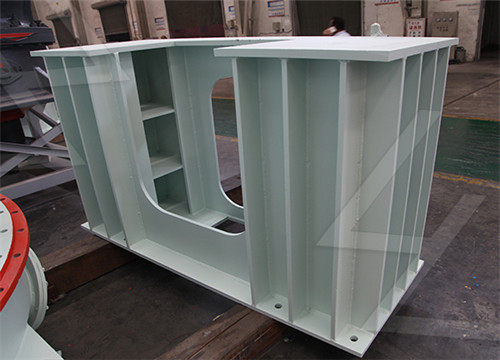
Assessment of the Performance of Grinding Circuit
202129 The ball mill performance was poor and could be indicated by only 5-9 % of< 125 µm (target product) in the discharge. This had a direct impact on hydrocyclones, where significantly poor

Fine grinding in a horizontal ball mill ScienceDirect
200741 Fine grinding in a horizontal ball mill T. Partyka,D. Yan Add to Mendeley https://doi/10.1016/j.mineng.2006.12.003 Get rights and content Abstract The fine
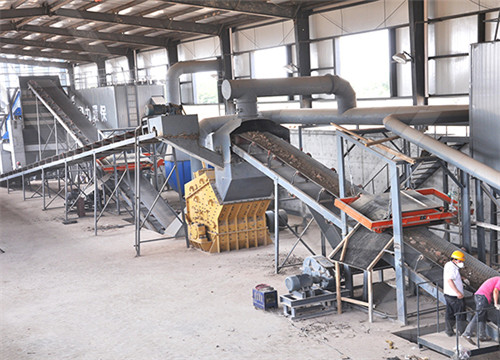
Minerals Free Full-Text Study on the Grinding Law of Ball
2022221 To solve the problem involved in the grinding of cassiterite–polymetallic sulfide ore in which fine grinding causes the cassiterite to be overground or coarse
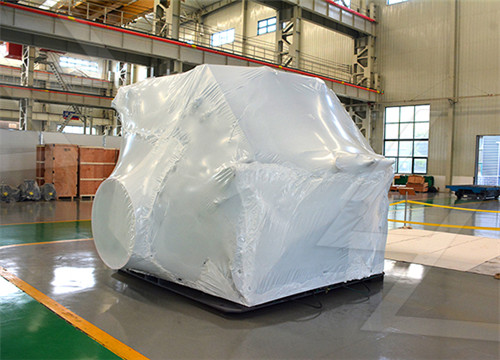
8 Pieces of Gold Mining Equipment to Get Gold Concentrates
2023527 Wet Pan Mill Yes, I am interested!. Wet pan mill, also called gold grinder mill, is a versatile ore grinding pan mill for processing gold, silver, copper, etc. As an affordable alternative to ball mills, wet pan mills are ideal and efficient equipment for ore beneficiation in small and medium gold processing plants.
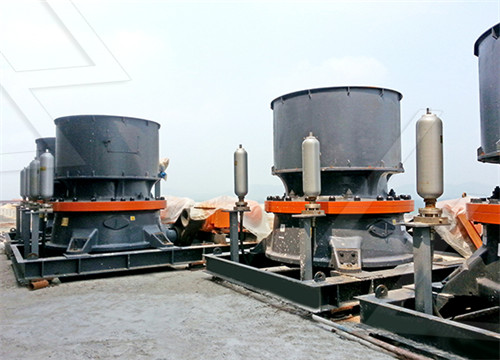
Procedure for determination of ball Bond work index in the
200911 Section snip Grinding kinetics in the Bond ball mill. Tests of grinding kinetics in the Bond ball mill (Fig. 1, Fig. 2) has shown that over a shorter grinding period, the process follows the law of first order kinetics R = R 0 e-kt where R = test-sieve oversize at the time (t); R 0 = test sieve at the beginning of grinding (t = 0); k: grinding rate

Ball Mill Mining Grinding Mill Mineral Processing
1 Introduction: The ball mill is a tumbling mill that uses steel balls as grinding media. Ball mills can be used in wet or dry systems for bulk and continuous milling, and are most widely used in small or large-scale ore
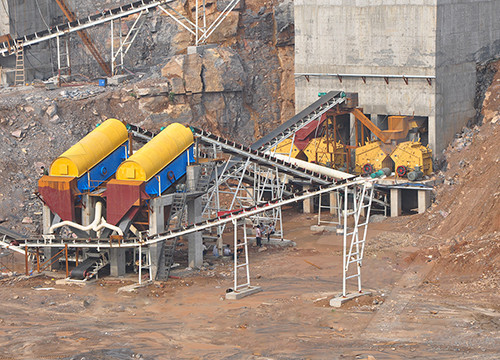
(PDF) Optimization and performance of grinding circuits: the
2020116 Previous work by Wikedzi (2018) concentrated on grinding circuit performance, with the case of Buzwagi Gold Mine (BGM). The survey data collected at BGM plant between April and June 2015 indicated
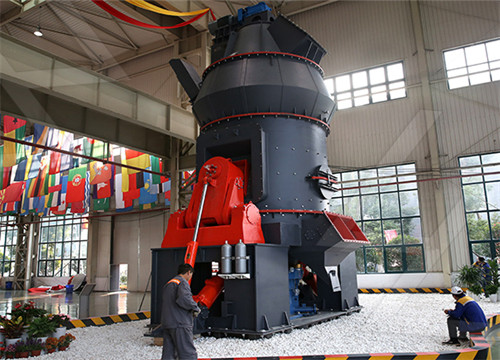
Investigation on Iron Ore Grinding based on Particle Size Distribution
2020528 The feed samples of X, Y, and Z iron ores were ground in the BBM (ball mill refers to a BBM of size 300 mm × 300 mm with smooth liners) to identify the PSD, BWI, and RT of each ore. Grinding experiments were conducted according to Bond’s standard test procedure [].For each iron ore sample, the RT taken to produce 250% circulating
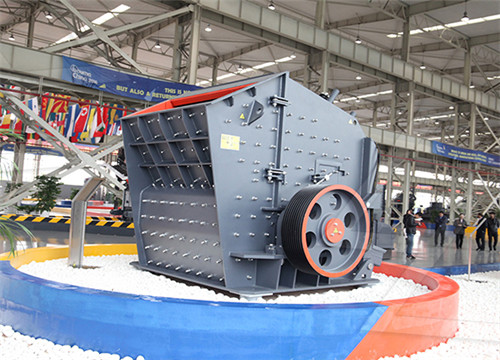
Top 10 Best Mineral Processing Equipment Fote Machinery
20231027 Ball Mill is the key equipment for grinding after the crushing process. Price: $5, 000/ Set (the lowest price) Materials: Quartz, plastic powder, carbon black, hematite, limonite, molybdenum ore, gold ore, iron ore, etc. (concentration: within 30%, granularity: within 1 mm). 10. Tailing Disposal Equipment High Efficiency Concentrator:

Assessment of the Performance of Grinding Circuit for Buzwagi Gold
202129 Ball mill feed and product particle size distribution for survey 1, 2 and 3 Figure 8 to Figure 11 and Table 11 to Table 13 present the results for the size distributions and some key performance
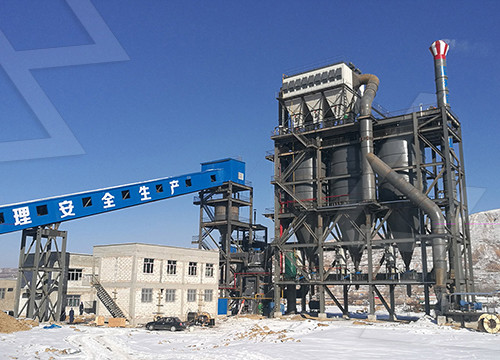
Grinding equipment for gold ore processing in Siberia
While the total grinding capacity was only utilised to 85 %, the ball mill already absorbed 17.4 MW of 18.0 MW. During the last years the process circuit also had to be adapted to changes of ore mineralogy. Coarser gold liberation size the fines of grind changed from originally 80 % < 74µm to 80 % < 130 µm. Gold enrichment was therefore
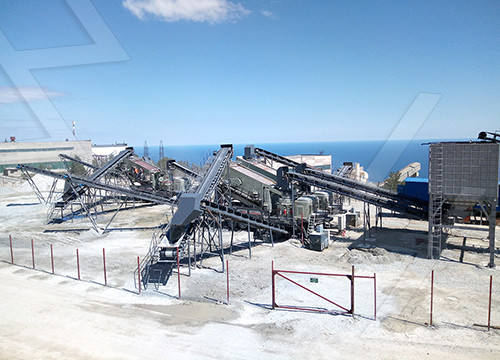
Comparison of energy efficiency between ball mills and stirred mills
200961 Four different laboratory ball mills and stirred mills have been tested to grind seven ore samples with feed sizes ranging from 3.35 mm to 150 μm. A case study on full scale operations of a 2.6 MW IsaMill replacing the existing 4 MW regrind ball mill at Kumtor Gold Mine in Kyrgyzstan is also included. This stone summarizes the major findings
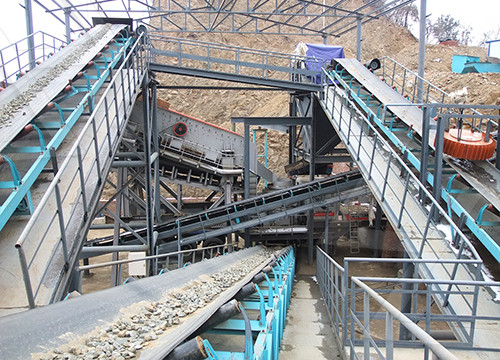
Impact of grinding aids and process parameters on dry stirred media
2018715 The use of dry stirred media mill has been speculated over the years with the aim of improving the energy efficiency in the zone of fine grinding that may lead to energy saving of the overall
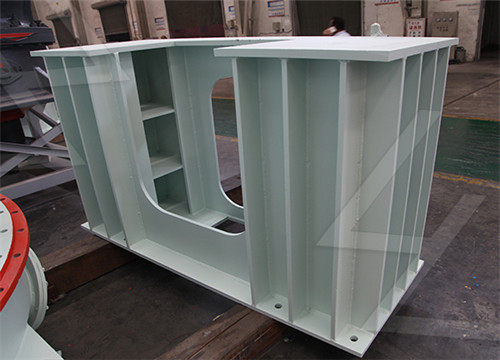
Fine grinding in a horizontal ball mill ScienceDirect
200741 Four different laboratory ball mills and stirred mills have been tested to grind seven ore samples with feed sizes ranging from 3.35 mm to 150 μm. A case study on full scale operations of a 2.6 MW IsaMill replacing the existing 4 MW regrind ball mill at Kumtor Gold Mine in Kyrgyzstan is also included. This stone summarizes the major findings
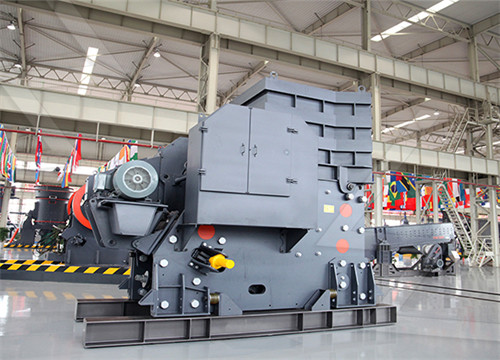
Ball Mill (Ball Mills Explained) saVRee saVRee
Crushed ore is fed to the ball mill through the inlet; a scoop (small screw conveyor) ensures the feed is constant. For both wet and dry ball mills, the ball mill is charged to approximately 33% with balls (range 30-45%). Pulp
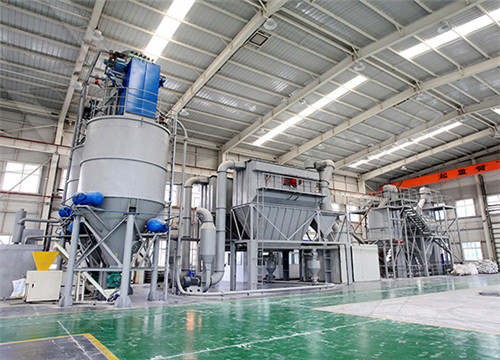
Buy Ore Ball Mill for Mineral Processing Iron
Ore Ball Mill. Output size: 0.074-0.89mm. Motor power: 18.5-480kw. Specification (mm): Φ750×750-Φ2700×4500. Applications: It is used for processing various grindable mineral materials, non-ferrous metal
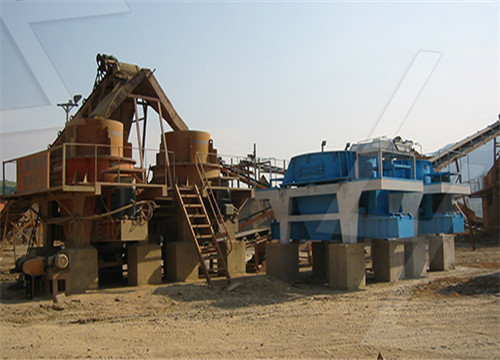
Fine Grinding as Enabling Technology The IsaMill
20231029 These features distinguish stirred mills as fundamentally different from both ball mills and Tower Mills, as demonstrated by Tables 1 and 2. Table 1 : Typical Power Intensities of different Grinding Devices Table 1: Power Intensity of Different Grinding Devices Ball Mill is a 5.6m D x 6.4m L @ 2.6MW Tower Mill is a 2.5m D x 2.5m L @ 520KW
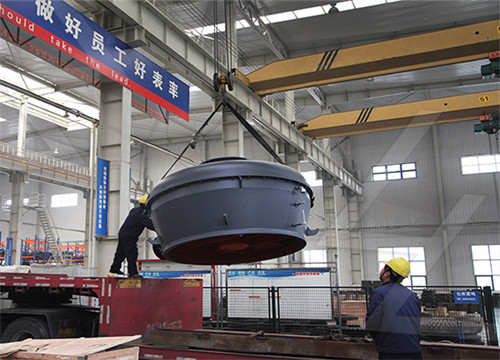
Consumption of steel grinding media in mills A review
201381 An estimated consumption of steel grinding media of around 600,000 tons p.a. in the 1980s already gives an indication of the scale of the problem (Malghan, 1982). Likewise, in the cement industry, as mills are supplied for ever increasing capacities, the ball size distribution and wear exact a tremendous effect on the profitability of producing

Laboratory Ball Mill for for continuous grinding operation
2023130 It could be adopted for ore grinding research and small amount of ore gringing for pilot ore dressing plant. Recently an UK Graphite mining company takes an inquiry on our Laboratory Ball Mill for the above aim. The structure of ball mill is mainly composed of the frame, feeding part (feeding ore bin, Swing feeder), snail feeder part,
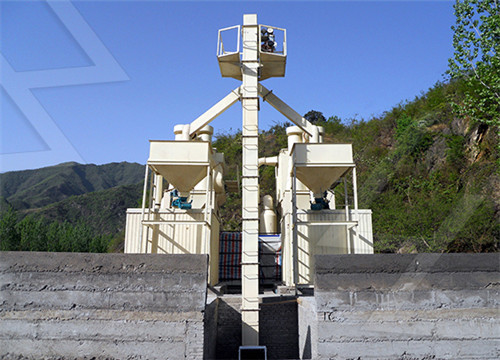
(PDF) Grinding Media in Ball Mills-A Review ResearchGate
2023423 The motion of grinding media in a ball mill is essential since it has a grea t impact on the breakage of ore parti cles. When the mill speed increa ses, the charge motion changes from sliding to
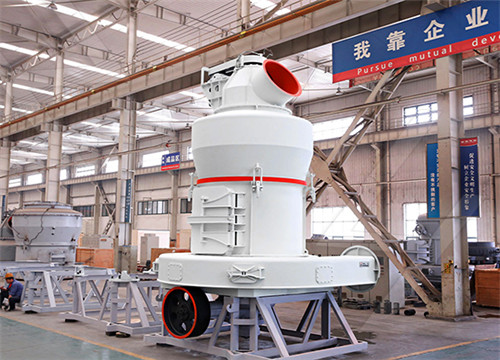
Experimental study on the grinding rate constant of solid materials
2002122 In this , we carried out batch grinding tests of silica glass, limestone and gypsum with a ball mill and investigated the effects of feed size and ball diameter on the grinding rate constant (selection function). The results are summarized as follows; 1. Variation of the dimensionless grinding rate constant with feed size was roughly
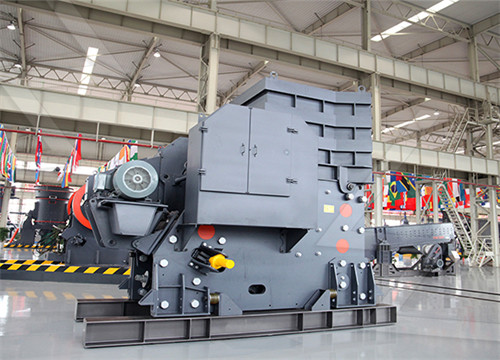
Copper ore grinding in a mobile vertical roller mill pilot plant
2015310 Promising results obtained from cement industry encouraged the test studies on mineral grinding. van Drunick et al. (2010) presented VRM pilot plant test results where zinc ore was ground. In his study it was concluded that the total specific energy of the AG/SAG-ball mill circuit, which was 20.11 kWh/t, was reduced to 11.40 kWh/t by using
كسارة الحجر معدات منجم الأخبار
معدات مطحنة قرب فايتيفيل نورث كارولاينا
آلة المحجر وبيع محطة كسارة في العراق
خرائط لمنازل بمساحة 100 م
مدرسة ابتدائية لمحجر الجرانيت
توفير التكلفة دائم استخدام قضيب مطحنة الرمال ماكينة
عدة كبريتات دراسة الكيمياء كريستال على تعويم المعدنية
الفك حجر محطم مخروط مصنع crosher 100 الهيدروكربونات النفطية lamilpa
إمدادات معدات تغذية السيليسيد الكالسيوم
لمحة عن شركة التعدين الإجمالية
وظائف وحدة تكسير الحجارة
الحديد المحمول الفك خام محطم للبيع في مصر
مرجع نسوي من الطاحونة على الخيط
تدفق الرسم البياني محطة كسارة الحجر
محطم للتكعيبي شكل الحصى
آلة طحن مطحنة الحجر شنغهاي للبيع خامات التعدين
كسارات مستعملة في مصر
تستخدم كسارة الحجر المتنقلة في المملكة العربية السعودية
آلة غسيل لتنظيف السجاد
تصميم واختيار محطة التكسير
الذهب ختم مطحنة للبيع جنوب أفريقيا
مطلوب آليات طحن الكوارتز html
نوعية ممتازة ارتداء جهاز تغذية لوحة سلسلة مقاومة
قطع غيار لكسارة الصخور باركر
شركة مناجم تعدين خام
تحتاج مصنع الحديد لبناء الفحم الروسي
حول لدينا
تأسست شركة Henan Lrate للعلوم والتكنولوجيا المحدودة التي تصنع معدات التكسير والطحن الكبيرة والمتوسطة الحجم في عام 1987. وهي شركة مساهمة حديثة مع البحث والتصنيع والمبيعات معًا.
على مدار أكثر من 30 عامًا ، تلتزم شركتنا بنظام الإدارة العلمية الحديث والتصنيع الدقيق والريادة والابتكار. الآن أصبحت LIMING رائدة في صناعة تصنيع الآلات المحلية والخارجية.